Generating better mutli-lattice transitions for manufacturing
Pamela Smith
Aug 31, 2023
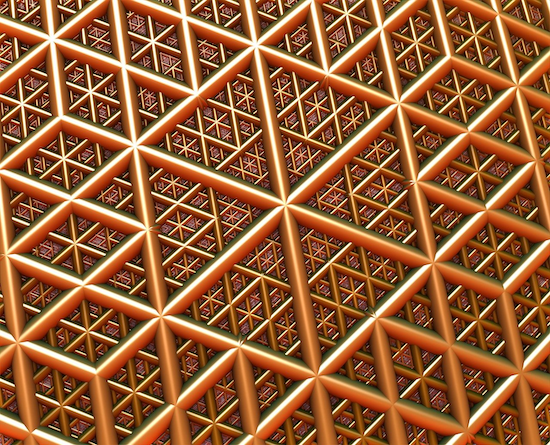
Many industries are looking to adopt additive manufacturing methods to create more flexible, higher performance parts for complex creations. Lattices are a material structure used to fill a 3D space using a repeating pattern that can help strengthen the final product.
PhD student Martha Baldwin, along with advisor Chris McComb and collaborator Nicholas Meisel from Penn State,conducted research that analyzed different variations of AI-generated multi-lattice structures. They found that the smoothness of AI generated transitional regions between different lattices was strongly predicted by the closeness of their endpoints in the “latent space” learned by the AI. It turned out that transitional intervals between the lattice structures are not the sole predictor of overall smoothness and continuity of the structure.
McComb, an associate professor of mechanical engineering, believes that this research provides an important look into creating smoother and more mass-conscious lattice structures as manufacturing develops.
“Anytime you put something on a shuttle or spacecraft, mass is so critical. You want to get rid of as much weight as you can.” McComb said. “Lots of different industries are adopting these methods to get parts that are going to be greener and more sustainable because they use less energy and material to produce. An important technique in achieving those goals is being able to flexibly create lattices.”
McComb discussed the importance of fine-tuning connections between lattices.
That’s what this work is—figuring out how to smooth out part design to not just make it look smooth, but also help ensure they’re in smooth properties. You don’t want the part to suddenly turn from concrete into a gummy bear.
Chris McComb, Associate Professor, Carnegie Mellon University
“What really becomes challenging is matching those lattices up and making sure that you have a smooth, continuous part design,” McComb said. “That’s what this work is—figuring out how to smooth out that part design and not just make it look smooth, but also help to ensure that they’re in smooth properties. You don’t want the part to suddenly turn, for example, from concrete into a gummy bear.”
According to McComb, the large sets of lattice data they needed to conduct this research didn’t exist at first. Baldwin took the lead in constructing a new dataset to support the research. They hope this new data will help develop design software in the future that can easily generate advanced lattice structures.
“It took lots of computation and lots of overheating computers,” McComb said. “We now have this data set, and we’re actually planning to publish that as well. If it was useful for us, it’s probably going to be useful for other folks too.”
This research was published in 3D Printing and Additive Manufacturing. Martha Baldwin, a Ph.D. candidate in mechanical engineering, and Nicholas Meisel, associate professor of engineering at Penn State University, were collaborators on this work.