Polymers, printing, and pathways
The optimized future of additive manufacturing
Olivia Olshevski
Jul 9, 2019
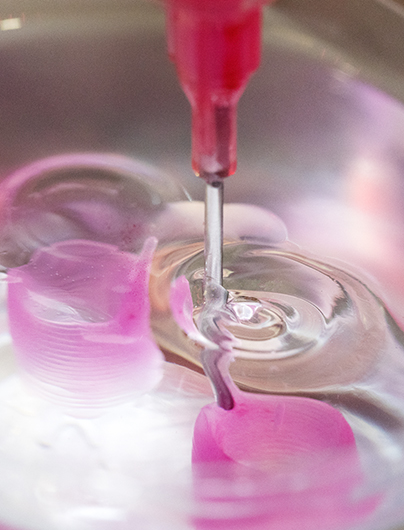
Source: College of Engineering
Additive manufacturing, biomechanics, design optimization, and polymer synthesis merge as researchers collaborate across disciplines.
Over the past few years, additive manufacturing, also known as 3-D printing, has been applied to a wide range of industries. This method enables manufacturers to create parts which overcome traditional manufacturing limitations while also maintaining a high performance level.
Despite its recent growth, additive manufacturing has only been applied minimally to the creation of polymers, as only very few polymers can be utilized in the method. In addition, the material properties of many polymers have orientations which differ from the printed part, ultimately sacrificing the mechanical integrity of the finished product.
To begin to extend the application to polymers (such as soft rubbers, eurythenes, epoxies, and other polymer composites essential to industrial applications), a group of Carnegie Mellon University faculty across multiple fields of engineering have come together to propose a transformative advance in polymers additive manufacturing. By creating a new method of 3-D printing (Freeform Reversible Embedding 3-D Printing, or FRE-3DP), they have produced an approach which enables many exciting possibilities, including the implementation of truly three-dimensional (non-planar) tool paths.
Each faculty member brings to the table their own expertise, enhancing the success of such a collaborative effort. While Adam Feinberg’s lab (Departments of Biomedical Engineering and Materials Science & Engineering) serves as the creator of FRE-3DP, Professor Michael Bockstaller’s lab (Department of Materials Science & Engineering) brings expertise in polymer synthesis. Additionally, Burak Ozdoganlar’s lab (Department of Mechanical Engineering) has focused on the multi-axis control requisite for the non-planar paths, and Burak Kara’s lab (Department of Mechanical Engineering) has developed design optimization approaches that leverage this novel non-planar printing capability.
This project is part of the Manufacturing Futures Initiative (MFI) which aims to bring engineering discoveries to manufacturing and commercialization in a collaborative, multidisciplinary environment. As a continuation from a funded MFI Year 1 project, its second year is focusing extensively on taking the proof of concept provided in the first year and expanding its applicability to a number of real-world situations.
Ultimately, the goal of this project is to take the technology already utilized within bioprinting and to expand it more broadly to other industrial applications. This technique is especially useful in the production of highly complex parts, as well as parts only created in small batches. Its applicability spans across the entire scale, from printing small medical devices to producing entire aerospace structures. In line with the MFI vision, this project aims to establish this method as the dominant 3-D printing platform used in industry.
FRE-3DP is a form of 3-D printing which prints objects inside of a gel bath, rather than printing in air. By doing so, the group is able to use materials previously unused in the field. Commonly, the printing material must be both extrudable and quick to harden; this ensures that the object, printed layer by layer, remains structurally sound. With FRE-3DP, the materials used can be greatly expanded, significantly increasing their reach within the industry. With the gel bath, soft gels can also be printed, as the soft support gel ensures that the printed structure does not collapse during the printing process. What’s more, the gel bath also serves as a chemical environment, providing opportunities for additional structural reinforcement through the inclusion of cross-linkers and other adhesives into the gel.
In addition to investigating this new form of 3-D printing, the group is also expanding the complexity of the structures which can be printed. Typically, 3-D printed parts are formed layer by layer, with each thin layer cured before the next one is added. In this way, the structural integrity is maintained, with each new layer being added to a cured (and therefore stable) layer below it. While this technique has been great in producing durable parts, it limits the printing process to planar geometries. To create more complex and non-planar geometries, the group is creating a printer which allows the part to be printed in any direction.
Though 3-D printers which travel in any direction may be a conceptually simple idea, the implementation requires extensive design optimization. With extruders that can move along all three axes and bent or rotating nozzles that allow for more unique angles, the main task of using these unique features lies at the heart of this design optimization. For example, the CAD file which the printer uses as a directions manual must use a printing path which does not incorporate intersections (as this can lead to both wasted and uneven distribution of material). This often requires careful design and consideration of the instructions given to the printer.
This multidisciplinary group has demonstrated just how powerful collaboration can be. With their combined expertise, they have begun to create a method of additive manufacturing which will essentially transform the field. More than increasing the potential products and uses of additive manufacturing, this will serve as the next step in making 3-D printing available to all aspects of industry and engineering.
Carnegie Mellon’s Manufacturing Futures Initiative (MFI) awards fund multidisciplinary, collaborative projects of two or more faculty members. MFI awards specifically support research incorporating machine intelligence into manufacturing environments.
Media contacts:
Emily Durham, edurham1@andrew.cmu.edu
Lisa Kulick, lkulick@andrew.cmu.edu